Tanker is a unique type of vessel with allows transporting liquid cargos in bulk. Generally accepted commercial classification divides tankers by cargo type into the following categories:
- Oil tankers (those, in turn, include – Crude Oil Tankers, Oil Product Tankers, Oil / Bulk / Ore Tankers (OBO), Ore / Oil Tankers (ORO);
- Chemical Tankers;
- LPG / LNG Carriers.
There are also other types of classifications and intricate details about each type of these vessels which we’ll discuss in this article.
Oil Tankers
Classification of Tankers by Deadweight
Classification of Tankers by Size
Interesting Facts about Tankers
Wage Rates on Oil Products Tanker
Chemical Tankers
History of Chemical Tankers
Classification of Chemical Tankers by Size
Types of Chemical Tankers
Top Chemical Tanker Accidents
Wage Rates on Chemical Tankers
Gas Carriers – LPG / LNG Tankers
History of Gas Carriers
Classification of Gas Carriers by Size
Types of Gas Carriers
Cargo Containment Systems
Interesting Facts about Gas Carriers
Wage Rates on LPG/LNG Tankers
Tanker Market Outlook for 2020 – 2021
The history of shipbuilding dates back thousands of years, while the first tanker was built only in 1877. The deadweight of M/T “Zoroaster” was only 250 tons and she was employed to transport kerosene in bulk from Baku to Volgograd (then Tsaritsyn). The key to such historical gap is in the unsolved engineering problem.
Large volume of liquid in a hold affected stability of a vessel. As a result, liquids were transported in barrels almost to the end of the 19th century. Moreover, there were no efficient pumps while wooden hulls inhibited normal storage of liquid cargo. Meanwhile, with the advent of steel vessels, division of the hull into separate tanks and invention of modern pumping systems the new industry was born.
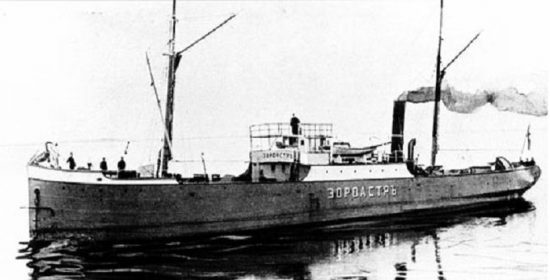
Today tankers are the most popular and profitable way to transport liquid cargoes. For example, according to U.S. Energy Information Administration more than 60% of all world crude oil is carried by sea.
OIL TANKERS
According to Statista.com more than 7,000 oil tankers operate in the ocean today. Most of them are crude oil carriers.
The SOLAS-74 provides general classification of oil tankers dividing them from the fire safety point of view into 2 categories:
- Tankers for transportation of crude oil and petroleum products with a flashpoint below 60 °C (140 °F) and a vapor pressure below atmospheric.
- Tankers for the transportation of petroleum products with a flash point above 60 °C (140 °F).
With regards to size, crude oil tankers also dominate. Oil Product Tankers that carry gasoline and other petroleum products usually have modester dimensions.
Classification of Tankers by Deadweight:
Category | DWT | Description |
GP (General Purpose) | 6000—16 499 t
(1.8 – 4.9 m gallons) |
Low-tonnage general purpose tankers. Often used to transport bitumen. |
GP (General Purpose) | 16 500—24 999
(4.9 – 7.5 m gallons) |
General purpose tankers for petroleum products. |
MR (Medium Range) | 25000—44999 t
(7.5 – 13.5 m gallons) |
Medium tonnage tankers. Used both as crude oil and product tankers in small waterways. |
LR1 (Large/Long Range1) | 45000—79 999 t
(13.5 – 24 m gallons) |
Large Range Class 1 tankers. These are employed for transporting crude oil and heavy oil products. |
LR2 | 80 000—159 999 t
(24 – 48 m gallons) |
Large Range Class 2 tankers. |
VLCC (Very Large Crude Carrier) | 160 000—320 000 t
(48 – 96 m gallons) |
Class 3 large tankers transport crude oil from production sites to refineries. |
ULCC (Ultra Large Crude Carrier) | Above 320 000 t
(above 96 m gallons) |
Also known as Supertankers. Carry crude oil over long distances. For example, from the Persian Gulf to refineries in America or Asia. |
FSO (Floating Storage and Offloading unit) | Above 320 000 t
(above 96 m gallons) |
These are Supertankers whish have been re-built or specially designed as floating oil terminals. Developed oil is stored at sea and transferred to smaller tankers.
FSO ASIA is the largest such vessel in existence. Her DWT is 441,893 tons and she operates in the Persian Gulf at the moment. |
Classification of Oil Tankers by Size:
Like the majority of vessels, dimensions of tankers subject to global navigational conditions:
Seawaymax:
These tankers can fit through a narrow system of locks of the St. Lawrence Seaway (a 2500-km-long (1553 ml) sea channel connecting the Atlantic Ocean with the Great Lakes in the USA). The maximum deadweight of a vessel passing by this route must not exceed 28,500 tons, length – 225.6 m (740 feet), width – 23.8 m (78 feet), draft – 8.1 m (8.08 m).
The reality is that only 10% of ordinary seagoing vessels can pass all 14 canal locks up to Lake Superior. Therefore, navigation is mainly carried out by special vessels built for this region.
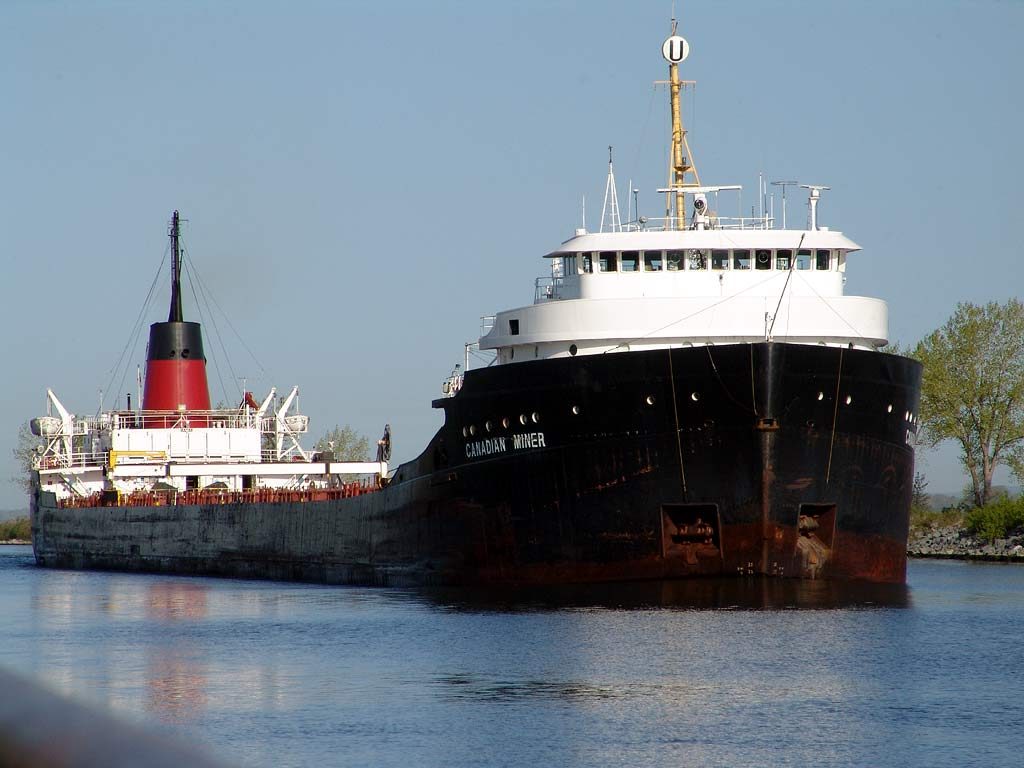
Panamax:
Dimensions of tankers in this category are limited by the size of the Panama Canal. The New Panamax Project aimed at expanding the narrowest channel cameras was completed in 2016. Now Canal can accommodate vessels with the length reaching 336 meters (1102 feet), a width of up to 49 m (161 f) and a draft of up to 18.3 m (59 feet). These impressive metrics replaced earlier allowed dimensions of 294 m (965 f) in length, 32.2 m (105 f) width and 12.6 m (43 f) draft.
This is especially good news for LPG-carriers going from the USA to Asia. According to DNV GL analytics, as of the end of 2017, 100% of all American NEO-Panamax gas carriers passed through the canal. Moreover, the Panamanian authorities have achieved a good speed of passing ships – 5.9 tankers per day.
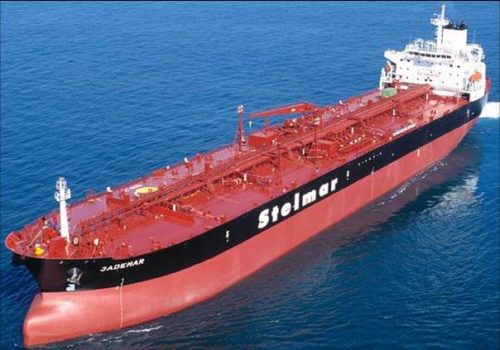
Aframax:
The term derives from the name of the Average Freight Rate Assessment (AFRA) system created by Shell Oil in 1954. Aframax tanker dimensions are usually up to 120,000 DWT, length – 253 m (830 f), width – 44.2 m (144 f). This is the most popular type of tanker at the moment. Armed with their compact dimensions they can work in most marine terminals of Northern, Black, Mediterranean, Caribbean seas; while their big capacity allows economizing on oil transit.
Suezmax:
The next common category of vessels is focused on the passage of the Suez Canal. After numerous expansions it is able to fit vessels with deadweight of up to 200,000 tons, a maximum draft of 20.1 m (66 f) with a width of 50 m (164 f) or a draft of 12.2 m (66 f) and a width of 77.5 m (253 f).
Suezmax tankers are widely used around the world, especially in West Africa, the Black Sea, Persian and Mexican Gulfs. Experts give Suezmax tankers a favorable prognosis for the future. More sophisticated refineries squeeze old players from the market, so more Oil Products Tankers are required; while the VLCC’s niche will shrink eventually.
In addition, these tankers show unexpectedly good financial results even in the time of Covid -19 pandemic. Frontline has announced that its average TCE (time charter equivalent) rate for a Suezmax rose up to USD 57 800 in Q2 2020 compared to USD 38 200 in the same period last year.
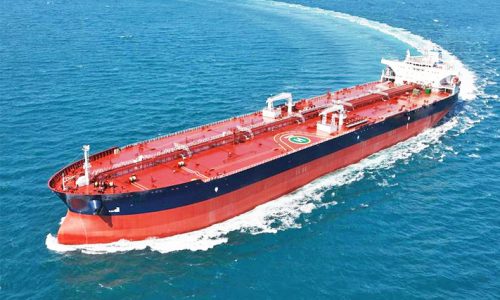
VLCC:
Large tonnage crude oil tankers (Very Large Crude Carrier) are also called Malaccamax tankers named after the Strait of Malacca, the main route connecting the Indian and Pacific Oceans.
VLCC dimensions are limited only by the minimum depth of the strait – 25 m (82 f). Therefore, the draft in this category does not exceed 20 m (66 f). The tanker deadweight is from 200,000 to 320,000 tons, the length is 330 m (1083 f), and the width is 60 m (197 f). VLCCs are common in the regions of oil production such as the Middle East or West Africa.
They transport crude oil to large buyers over long distances. However, the recent unprecedented economic situation has turned 80% of crude oil carriers into temporary floating storages.
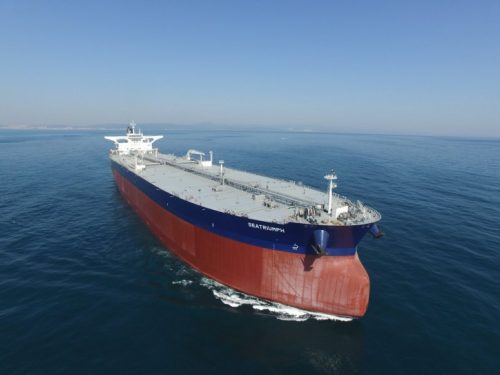
ULCC:
Ultra-large crude carriers (Ultra Large Crude Carrier), also known as Supertankers, have deadweight of 320,000 to 550,000 tons, a length of 415m (1362 f), a width of 63m (207 f) and a draft of more than 35m (115 f). Such vessels require special terminals and usually transport oil from the Persian Gulf to major ports of Asia, America and the Northern Europe.
Interesting Facts about Tankers:
-
Knock Nevis
M/T Knock Nevis is the largest oil tanker in history, built in 1979 in Japan. Its deadweight was 564.763 tons and length – 458 meters (1503 f). The tanker sunk during the Iran-Iraq conflict, but was restored later and continued operation. Scrapped in 2010.
-
Mega Yacht Made of Tanker
The Austrian design bureau MOTION Code: BLUE recently presented the revolutionary design of a superyacht based on the Suezmax tanker. The concept is called “Imara”. It has a length of 280 meters (919 f), so there is enough space for several helidecks, a garden of palm trees, a concert hall, bars, terraces, numerous apartments. The owners and guests of the superyacht will saunter along the decks in spherical electric cars.
Tanker – Megayacht; Credits to Opensea.pro -
The Game Changing Accident
The disaster that transformed the world of oil transportation happened on March the 24th, 1989 when M/T Exxon Valdez grounded in Alaska. The hull was ripped open; and 144,000 tons (43 m gallons) of oil spilled into pristine waters of Prince William’s Strait.The consequences of this environmental disaster have been observed over the next 25 years. Meanwhile, shipping industry responded by adoption of the Oil Pollution Act 1990 which has a huge effect on the operation of modern tankers.
-
The Black Gold Project
There is a project with such alluring name in the countries of the Persian Gulf. The Black Gold Project involves transformation of an old oil tanker into a multifunctional complex with business and entertainment centers. The tanker will be moored off the coast and a promenade will pass through it.
Black Gold Project; Credits to Opensea.pro -
Recent Big Accident
Despite all the precautions, incidents with oil tankers are still inevitable. The last big tragedy happened in January 2018. The Iranian tanker M/T Sanchi were on her way to South Korea with a cargo of light oil (136,000 tons or 41 m gallons) when she collided with a bulk carrier off the coast of China. The next day the vessel “suddenly” caught a fire throwing a kilometer high pillar of flame and smoke into the sky. There were 32 crew members on board, only three bodies subsequently were found. The public has criticized the Chinese authorities severely for their lack of efforts to save the crew and prevent environmental damage.
M/T Sanchi_Accident; Credits to AFP/Getty Images
The oil spill affected the main fishing areas of China, but was difficult to assess and eliminate. The light oil is transparent and merges with the surface of the water. The Sanchi’s fuel oil slicks were 15 and 18 km long. She sank 8 days later.
Wage Rates on Oil Products Tanker
While it’s quite easy to investigate earnings of the industry itself, it requires a more scrupulous gaze to figure out salary rates on a vessel. Meanwhile, there are a lot of vacancies on Oil Products Tankers for all positions and nationalities, so the approximate figures can be picked.
Wage rate on Oil Products Tanker for Eastern European crew are:
Position |
Wages, USD |
Master | 10 500 – 13 500 |
Chief Officer | 7 600 – 8 200 |
2nd Officer | 3 300 |
3rd Officer | 2 800 – 3 000 |
Chief Engineer | 9 500 – 10 000 |
2nd Engineer | 7 700 – 8 000 |
3rd Engineer | 3 700 – 4 000 |
4th Engineer | 2 800 – 3 500 |
ETO | 5 000 – 5 300 |
Pumpman | 2 200 – 2 400 |
Fitter | 2 100 – 2 500 |
Cook | 1 600 – 2 000 |
Bosun | 1 800 – 2 000 |
AB | 1 250 – 1 500 |
Oiler | 1 250 – 1 500 |
OS | 1 300 – 1 500 |
Wiper | 1 000 – 1 100 |
Deck/Eng. Cadet | 450 – 500 |
*There is a Salary Gap between Nationalities in Maritime Industry meaning that although officers earn compatible sums regardless of their origin, ratings’ wage rates still reflect their passport details. For instance, Asian deck and engine ratings will get USD 200 – 500 less compared to Eastern Europeans; while American or EU seamen tend to earn USD 200 – 500 more than their colleagues from Russia, Ukraine and so on.
CHEMICAL TANKERS
This is a special type of vessel designed to transport chemicals in liquid form without packaging. The history of chemical tankers dates back only 60 years. Initially, these were oil tankers built in the late 40s of the 20th century and rebuilt to transport vegetable oils and grease. The first purposefully built chemical tanker made its way from the Great Lakes to the Northern Europe in 1959.
The construction of chemical tankers begins in the 60s, but the real boom unwraps in 70s with the rapid development of the chemical industry. This is the time when the double bottom structure, stainless steel tanks appear and technologies of coverage are improved. Cofferdam and modern cargo systems are introduced along this period as well.
New players – “Asian Tigers” arrive to the market in the 90s. The development of chemical industry in Southeast Asia brings up shipowners from Thailand, Taiwan and South Korea and diversifies geography of the routes. The fleet of tankers also updates significantly during this decade.
In the 21st century the industry is developing against the background of strict environmental and tax restrictions. The market is controlled by a powerful oligopoly – 14 large companies control the bulk of the traffic.
Classification of Chemical Tankers by Size
The size of chemical tankers is usually smaller compared to the oil giants. By deadweight, chemical carriers are divided into the following categories:
- Inland Chemical Tankers – 500 – 4 000 tons (ships for inland waterways, river chemical tankers);
- Coastal Chemical Tankers (Short Sea Tankers) – 3000 – 10,000 tons (ships for coastal navigation). These small chemical tankers appeared only in the 80s when it became expedient to build small vessels specifically for the transportation of chemical products.
- Deep Sea Chemical Tankers – 10,000 – 75,000 tons. The most common category of tankers nowadays.
Types of Chemical Tankers
All activities of this industry are strictly regulated by MARPOL and the International Bulk Chemical Code (IBC Code) which divides chemical carriers into 3 types:
Type 1
such tankers are designed for the carriage of goods representing the maximum danger to the human health and environment. Transportation of such cargo requires the stringent measures to prevent leakage i.e. double-hull or bottom system in case of a collision or grounding of a tanker.
There are few such super-dangerous goods in Chapter XVII of the IBC Code. For instance, these are such agents as chlorinated paraffin, chlorosulfonic acid (classified as chemical weapon), organic solvent dodecane, etc. As a result of so many precautions, Type 1 tankers are not as popular in the market as other categories.
Type 2
This type of tankers carry cargoes that pose a serious threat to the environment and human health. Therefore, require an adoption of significant protective measures to prevent leakage on board. This is the most commonly used type of chemical tankers. They transport everything from acids to alcohols and petroleum products. Tankers of the second type also have double hull.
Type 3
Vessels of this type transport cargoes that are listed in Chapter XVII but present little danger to the environment or human health. Tank and hull structures require moderate precautionary measures. Therefore, one longitudinal bulkhead is sufficient for such tankers. These vessels are reserved for transportation of molasses, vegetable oils, glycerin and so on.
Top Chemical Tanker Accidents
Such attention to safety is understandable since even a single accident on chemical tanker demonstrates the monstrous threat these vessels pose to all living:
M / T Bow Mariner:
The tragedy of Bow Mariner chemical tanker on February the 28, 2004 killed 21 people. The Singapore flagged vessel was going from New York to Texas with a cargo of industrial alcohol and other chemicals on board.
They were not far from the coast of Virginia when the captain has ordered to open the lids of 22 tanks for some inexplicable reason. As a result, combustible vapors were mixed with an air and a fire occurred on the deck. Its precise causes are still unknown. The investigation considered different versions from a mechanical spark to smoking and sabotage.
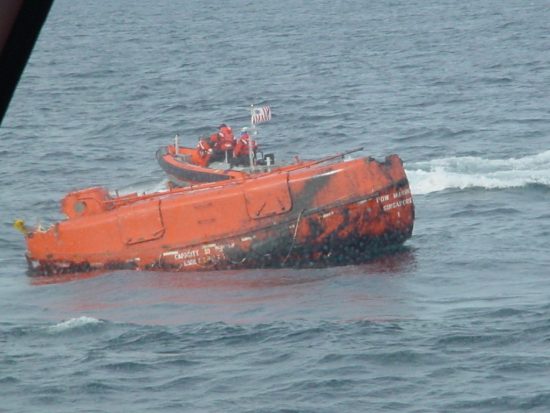
In any case, two powerful explosions occurred 2 minutes apart from each other. The tanker was severely damaged and sank after an hour and a half spilling out all 11,000 tons (3.4 m gallons) of technical alcohol, 730 tons of hydrofluoroolefine (dangerous refrigerant) and a fuel.
As the expertise revealed later, it had not been only captain’s actions which have led to the tragedy, but also the poor state of rescue equipment. As a result, three crew members were officially pronounced dead; and 18 are still listed as missing.
M / T levoli Sun:
Another well-known shipwreck in the industry occurred due to the entirely different reasons. The vessel of the Italian shipowner was caught by a storm in the English Channel on October the 30th, 2000 near the island of Alderney.
A strong wave swept the nose of chemical tanker; the vessel lost stability and drowned. There were 6000 tons (2 m gallons) of hazardous chemicals, incl. styrene (poisonous liquid for the production of plastic, foam and napalm), isopropanol (a polymer that is part of acetone), butanone (a powerful solvent) onboard of the 115 meter (377 f) tanker.
Fortunately, thanks to the coordinated actions of the crew and costal services, human victims were avoided that time, but the ecological situation was complicated by the fact that all these substances did not dissolve in water.
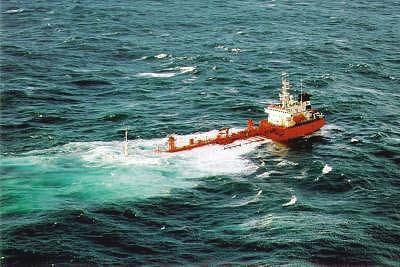
Wage Rates on Chemical Tankers
Salary rates on Chemical Tankers are usually higher compared to Oil Tanker industry. Futhermore, Chemical tanker jobs usually offer more favorable conditions (shorter terms, loyalty and training programs) in exchange for higher potential risk.
Usual wage rates there are:
Position |
Wages, USD |
Master | 12 000 – 12 500 |
Chief Officer | 9 800 – 10 000 |
2nd Officer | 4 000 – 4 200 |
3rd Officer | 3 000 – 5 300 |
Chief Engineer | 11 500 – 13 000 |
2nd Engineer | 9 000 – 9 500 |
3rd Engineer | 4 000 – 4 200 |
4th Engineer | 3 500 – 4 100 |
ETO | 5 500 – 6 000 |
Pumpman | 2 300 – 2 500 |
Fitter | 2 100 – 2 500 |
Cook | 1 700 – 2 000 |
Bosun | 1 800 – 2 000 |
AB | 1 250 – 1 500 |
Oiler | 1 250 – 1 500 |
OS | 1 300 – 1 500 |
Wiper | 1 000 – 1 100 |
Deck/Eng. Cadet | 500 – 600 |
Currently, there are more than 5,000 chemical tankers in the ocean. Their number has increased by more than 2.5 times since 2008; and analysts predict this industry to continue active growth until 2025 due to the rapid development of the chemical industry around the world, high demand for vegetable oils and fats and slowdown in oil production; although Covid-19 pandemic has definetely taken its toll on the industry.
GAS CARRIES – LPG/LNG TANKERS
Gas carriers are divided into two large groups:
LPG tankers that specialize in transporting such gases as butane, propane, butadiene, propylene, vinyl chloride monomer and even liquid ammonia; and LNG tankers carrying liquefied natural gas – methane and ethane.
History of Gas Carriers
The history of the liquefied gases transportation has begun in 1929 when Shell temporary re-designed M/T Megara for LNG transit. Then, M/T Angnita (DWT 4500 t) was built at Dutch shipyards in the 30s. She could simultaneously carry crude oil, LNG and sulfuric acid in her tanks.
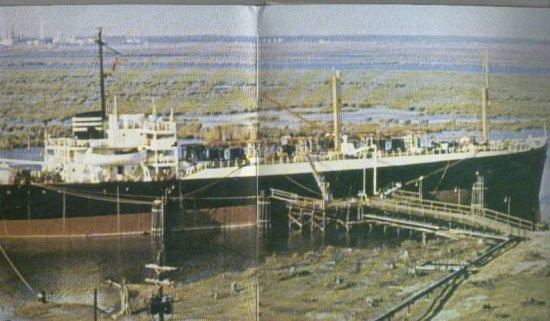
However, the real birth date for the industry of liquefied gas shipping is January the 25, 1959 when tanker M/T Methane Pioneer (DWT 5034) is specially re-built from a cargo ship and makes its first journey from Louisiana to Convey Island in the UK.
The project becomes commercially successful. So, Conch International Methane Ltd, inspired by the success of its first tanker, adds 2 large (27,000 m3/954000 cu ft) and technically advanced LNG carriers to its fleet in the early 60s. Ships work on gas shipments from Algeria to the UK at that time.
In the 70s, gas tankers’ development associates with the United States which export gas from fields in Alaska to Japan. During this period the US government orders 16 major LNG carriers at Swedish shipyards.
This is the legendary time when gas carriers become 5 times bigger, modern design of cargo tanks is introduced (Moss Rosenberg cargo containment spherical system); and shipyards in Norway and South Korea join the construction running.
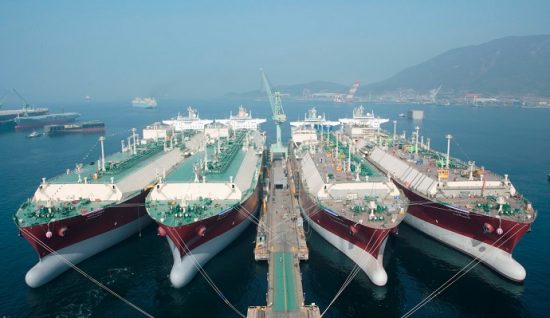
In the 80s and 90s Australia, Qatar and Russia take over the gas export initiative. The need for “blue fuel” and production are growing, so respectively is multiplying the size of LNG carriers.
In 1999 Samsung Heavy Ind. builds the largest and most expensive methane carrier in the world at that time. It can carry 138 378 m3 (4 876 772 cu ft) of gas, boasts a length of 279 m (915 ft) and is equipped with a new membrane tank system. But this record is already beaten. The Qatar – Max tankers project has been presented in 2003. These LNG carriers can carry up to 266,000 m3 (9 393 701 cu ft) of gas.
Today China’s state-controlled Hudong-Zhonghua shipyard is building the largest LNG carrier in the world. It will be able to carry 270 000 m3 (9 534 960 cu ft) of gas. In a view that Shanghai alone imported 600 million cubic meters of gas in January last year (4 Yamalmax tankers a month) it seems like a reasonable investment indeed.
Size Classification:
500 – 6,000 m3
17 657 – 211 888 cu ft |
Small fully pressurized gas carriers. They are used to carry propane, butane and ammonia at ambient temperatures. There are usually 2 cylindrical tanks at these vessels. |
1 000 – 12 000 м3
35 314 – 423 776 cu ft |
Gas carriers for the ethylene transportation. Gas is carried at atmospheric pressure, but is cooled to -104°C (-155° F). |
5 000 – 100 000 м3
176 573 – 3 531 466 cu ft |
Fully refrigerated LPG carriers; such vessels are employed for transportation of liquefied petroleum gases at atmospheric pressure and temperature -55°C (-67°F). |
40 000 – 130 000 м3
1 412 586 – 4 590 906 cu ft |
Isolated methane carriers of large displacement. LNG is transported at atmospheric pressure and at a temperature of – 163°C (-261°F). |
145 000 – 154000 м3
5 120 626 – 5 438 458 cu ft |
Conventional LNG carrier – general purpose methane carrier. |
172 000 м3
6 074 122 cu ft |
Yamalmax is a separate class of LNG carriers. Its dimensions are limited by the size of the approach channel of the port of Sabetta on the Yamal Peninsula.
The maximum depth there is only 15 m (49 ft), so the leading vessel M / T Christophe de Margerie (named after the President of Total) has a draft of 13 m (43 ft), but carries 172,600 m3 (6 095 311 cu ft) of gas and boasts an impressive 299 m (981 ft) in length and 50 m (164 ft) in width. Vessels of this class can also go independently through compact Arctic ice with a thickness of up to 1.7 m (6.54 ft). |
210000 – 216000 м3
7 416 080 – 7 627 968 cu ft |
Q-Flex or Qatar-Flex is a class of gas carriers developed in the early 2000s by ExxonMobil, Gas Transport-Technigas and Qatargas. Unlike its predecessors, Q-Flex tankers are equipped with 5 shorter and higher membrane tanks of the GTT * system which allows them to carry more cargo without losing stability. |
263000 – 266000 м3
9 287 757 – 9 393 701 cu ft |
Q-Max tankers repeat the Qatar-Flex tanker design in larger scale. The largest LNG gas carrier today is M /V Mozah. It was launched in 2008, has a length 345 m (1132 ft) and carriers 266 000 m3 (9 393 701 cu ft) of natural gas. The tanker was built by Samsung Heavy Industries (South Korea) and is operated by Qatargas II company. |
Gas carriers’ operations are regulated by the International Gas Carrier Code (IGC Code) which classifies these vessels according to hazard potential:
- 1G Type. Vessels are designed to carry chlorine, methyl bromide, sulfur dioxide and other gases specified in Chapter XIX of the IGC Code. These gases pose the greatest hazards to the environment, so their transportation requires maximum precautionary measures.
- 2G Type. These gas carriers transport cargoes that require significant protective measures to prevent gas leakage.
- 2PG. General type gas carriers. Such tankers have a length of up to 150 meters; and the safety requirements for their tanks are moderate – a pressure of at least 7 bar and a temperature of no more than -55 ° C (-67°F) for the cargo system.
- 3G Type Gas Carriers can carry cargo with moderate security measures.
Cargo Containment Systems:
Tanks design of gas carriers is worth exploring as well. When in contact with cooled and liquefied gas the metal becomes fragile and brittle, so gas tanks are made of expensive alloys such as invar (iron and 36% nickel), nickel steel (9% nickel), chromium-nickel steel (9% nickel, 18% chromium) or aluminum alloys. There are following types of cargo tanks: integral tanks, independent, membrane, semi-membrane and internal insulation cargo tanks.
The most widely used cargo containment systems are spherical systems of Moss-Rosenberg and membrane containment systems.
Moss-Rosenberg System:
The technology was first used at the Höegh plant in Norway for the LNG carrier M/T Norman Lady and dominated the market until the late 90s.
Spherical tanks are built separately and then mounted on the hull and fixed with a metal band along the line of the equator of the tank. Then, a procedure of heat insulation and covering of the tank with a metal body is conducted. Profound insulation and double enclosure ensure safety of the structure; while separate building reduces the cost. However, manufacturers have been favoring membrane systems for a while now since it allows avoiding the problem of cooling a large area of aluminum.
Membrane cargo containment systems:
When developing super gas carriers, engineers had to solve the problem of the safe and cost-effective transportation of liquefied gas, while retaining a small draft of future giants. Most of all these requirements are met by membrane-type tanks which currently occupy 57% of the market. 3 most popular types are:
- * GazTransport – the primary and secondary membranes are flat, made of invar steel;
- Technigaz Mark III – tank casing is made of stainless steel or aluminum wafer panels.
- CS1 – a combination of the above two systems. GazTransport invar panels are installed as the primary membrane, then 3-layer Technigaz membranes (sheet aluminum between two layers of fiberglass) as secondary insulation.
Interesting Facts about Gas Carriers:
-
Energy Content of LNG Tanker
The LNG’s energy content inside the tanks of modern Q-Flex gas carrier equals 60 bombs dropped on Hiroshima.
-
Major LNG Companies in the World
According to VesselsValue, 5 major shipowner companies in the industry now control up to 20% of all global LNG shipments. The list includes: Qatar Gas Transport Co (or Nakilat), Mitsui OSK Lines, Teekay, Maran Gas Maritime and the NYK Line. Their combined fleet consists of 110 vessels with a total cargo capacity of 19.5 million m3 (688.6 million cu ft).
-
Energy Potential of LNG Tanker
The energy contained in the tanks of two large LNG carriers is enough to boil 4 such lakes as Loch Ness or evaporate water from it completely.
-
LNG Fuel
LNG carrier usually loses about 0.1% of cargo daily due to evaporation. In 2000s LNG Reliquefaction System was introduced in order to reduce transportation losses, but at present it is more reasonable to utilize evaporating gas as a fuel for the vessel itself.
-
LNG for Middle East
The Middle East countries are in the list of LNG importers despite an active oil and gas production in the region due to undeveloped pipeline infrastructure. Therefore, it appeares more profitable for the United Arab Emirates, Kuwait, Egypt, Turkey and other countries to receive liquefied fuel by sea then to receive it from nearby Qatar by pipes.
-
What if LNG Tanker Blows Up?
If the ignition occurs on the gas carrier it will be impossible to extinguish the fire until the cargo burns itself out completely. In the event of a modern gas carrier’s explosion close to the shore the impact zone will be 190 km2 (73.3 sq ml).
-
The Most Serious Accident with LNG
The most serious accident in the industry occurred in November 1974. LPG tanker collided with a cargo ship in the port of Tokyo. This led to a massive explosion onboard, 34 seafarers died instantly.
Remains of the tanker which also carried some ligroin were towed out of the bay and drowned with torpedoes launched from a submarine, but an underwater burning continued for 20 more days. -
Terrorist Attack on LNG Tanker
Opinions are voiced occasionally that gas carriers may become a convenient target for terrorist attacks. The plot of Syriana movie revolves around this kind of story.
It features a Pakistani terrorist who hijacks and attempts to blast a LNG tanker. George Clooney won an Oscar for the Best Supporting Actor in Syriana in 2005. -
Top Ship-to-ship LNG Transfer
One of the world’s most impressive ship-to-ship Liquified Natural Gas (LNG) transfers happened on January 2 – 4, 2019 in Turkish port of Dortyol. FSRU Botas is moored there (the world’s largest Floating Storage Regasification Unit).
Botas is 345 meters (1132 ft) long and stores 263,000 m3 (9 287 757 cu ft) of natural gas. A 315-meter (1034 ft) Al Sadd supertanker approached FSRU with LNG cargo (206,000 m3) (7 274 821 cu ft) from Qatar. It took 2 days to pump over the gas from the LNG carrier.FSRU BOTAS; Credits to LNG World News -
FLNG Shell Prelude
FLNG Shell Prelude is the largest floating object in the world. It is a floating complex for the production, processing, storage and offloading of natural gas in the sea. The length of its deck is 500 meters (1640 ft or 4 soccer fields), 74 m wide (243 ft), and 100 m (328 ft) high. The giant was built to develop hard-to-reach gas fields 200 km (124 ml) off the coast of Western Australia and will produce 5.3 million tons of LNG per year.
Wage Rates on LPG/LNG Tankers
Salary rates on Gas Carriers are the most impressive in the industry today competing only with drilling earning. In addition, LPG/LNG jobs usually provide great working conditions as vessels are new and require stringent safety measures. The latter two factors usually entail advanced accommodation and profound career development plans for the crew.
Average LPG/LNG Tanker wage rates are as follows:
Position |
Wages, USD |
Master | 13 200 – 13 400 |
Chief Officer | 10 800 – 11 000 |
2nd Officer | 3 800 – 4 200 |
3rd Officer | 3 000 – 5 300 |
Chief Engineer | 12 000 – 12 500 |
2nd Engineer | 9 500 – 10 000 |
3rd Engineer | 4 200 – 4 300 |
4th Engineer | 3 600 – 4 100 |
ETO | 7 000 – 8 200 |
Gas Engineer | 6 700 – 6 800 |
Pumpman | 2 600 – 3 200 |
Fitter | 1 900 – 2 200 |
Cook | 1 700 – 2 000 |
Bosun | 1 900 – 2 200 |
AB | 1 500 |
Oiler | 1 600 – 1 800 |
OS | 1 300 – 1 500 |
Wiper | 1 000 – 1 100 |
Deck/Eng. Cadet | 500 – 700 |
As of 2019 there were only 1,800 gas carriers in the world, but their share is growing steadily. Gas tends to replace oil as an efficient source of energy; and the market share of companies specializing in gas production, transportation and processing is expanding.
Tanker Market Outlook for 2020 – 2021
Oil Tankers Market Prognosis
During spring 2020 oil demand plummeted due to Covid-19 pandemic and massive shutdowns all over the world. Onshore terminals have reached their maximum capacity and tanker shipowners were approached to provide their vessels as floating oil storages.
Therefore, freight rates had remained high despite the low demand for oil up until April; but now it has already been catching up with the oil tanker market. Demand for oil products is historically low dragging freight rates along.
Oil Demand Falling Throughout 2020
Although, it is expected that oil products’ consumption will recover a bit by the end of the year, it still will be way below its normal rate. BIMCO’s chief shipping analyst, Peter Sand, says that tanker market is facing a ‘gradual easing of the pain’ all over the next 2 years.
LNG Tanker Market Forecast
It seems the same fate awaits LNG market as experts claim that the global natural gas consumption has dropped 4% in 2020. All regions are impacted; especially Europe which is a mature market that has lived through the mildest winter in years and was hit by the corona-virus pandemic and lockdowns afterwards.
Analytics say that although the demand for LNG as well as LPG will restore gradually, the Covid-19 – driven crisis will impede development of the Gas Carriers market for some time. It will result in 75 bcm of lost annual demand by 2025, which equals the global annual increase in demand in 2019. So, the pandemic will have thrown the market 6 years back.
Chemical Tanker Market Outlook
It appears that Chemical tankers market copes better than most. Reputable Global Chemical Tanker Shipping Market Report, published in April 2020, states that the size of the global market of chemical tankers was USD 2 427 140 million in 2019 and it is expected to reach USD 2 789 460 million by the end of 2026, with a CAGR (Compound Annual Growth Rate) of 2.0% during 2021-2026.
The demand for chemical products used to be stable even throughout the Covid-19 pandemic (according to American Chemistry Council (ACC) 96% of all manufactured goods are directly or indirectly dependent on the chemical industry).
However, falling demand for Consumer Goods has taken its toll on the chemistry production and supply markets. Canadian giant Methanex, for instance, has closed its huge methanol plants in Trinidad and Tobago and Chile.
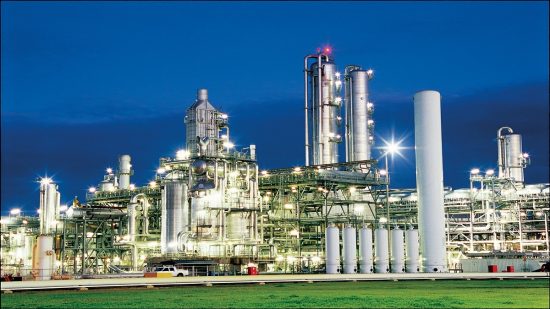
Meanwhile, inorganic chemistry appears to be affected the most by the corona-virus pandemic. These chemicals are used in metal processing, mining and as fertilizers, so their production fell by 6.7% in April 2020 as industries were shutting down.
The reduced demand has already entailed lower charter rates and tendency to employing small and medium-sized vessels. Today chemical tankers market is weighted down by other industries, but experts hint that the market will restore by 2022.